静电喷塑工艺解析:提升涂层附着力与均匀性的核心技术
静电喷塑(Electrostatic Powder Coating)是一种、环保的表面处理技术,通过静电吸附原理将粉末涂料均匀附着于工件表面,经高温固化后形成致密涂层。该工艺因其涂层附着力强、均匀性好、材料利用率高、无溶剂污染等优势,广泛应用于家电、汽车、建材、五金等行业。本文将从工艺原理、关键技术、优势分析及优化方向四个方面,解析静电喷塑如何实现涂层性能的突破。
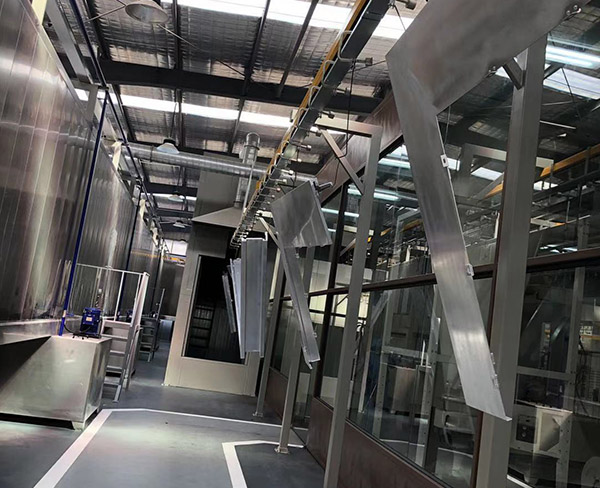
一、工艺原理:静电吸附与熔融流平的协同作用
静电喷塑的核心在于利用静电场力实现粉末涂料的定向沉积。其流程可分为四个阶段:
- 粉末充电:通过高压静电发生器使喷枪与工件之间形成电场,粉末颗粒在喷枪内部或喷出瞬间被电离空气摩擦带电,带电量通常为0.1-1mC/kg。
- 静电吸附:带电粉末在电场力作用下定向飞向接地的工件表面,形成均匀的粉末层。工件边缘因电场集中效应吸附更多粉末,需通过工艺控制避免“法拉第笼效应”导致的涂层厚度不均。
- 熔融流平:吸附后的粉末经180-220℃高温烘烤,树脂熔融并包裹颜料、填料,在表面张力作用下流平,形成光滑致密的涂层。
- 交联固化:树脂分子在催化剂作用下发生交联反应,形成三维网状结构,赋予涂层优异的机械性能和耐化学性。
二、关键技术:四大要素决定涂层质量
- 粉末涂料性能
- 树脂类型:环氧树脂提供强附着力,聚酯树脂增强耐候性,丙烯酸树脂提升光泽度。
- 粒径分布:D50粒径控制在20-50μm,过细易团聚,过粗影响流平性。
- 流平剂与助剂:添加0.5-2%的丙烯酸流平剂可降低表面张力,改善橘皮现象。
- 静电喷涂设备
- 喷枪设计:采用涡旋式或摩擦式喷枪,提高粉末带电效率。例如,摩擦喷枪通过尼龙管摩擦使粉末带电,适用于对电导率敏感的工件。
- 供粉系统:文丘里泵与流化床组合实现均匀供粉,压力控制在0.05-0.1MPa,避免粉末结块。
- 回收装置:旋风分离器与滤芯回收器协同工作,回收率可达98%以上,降低材料成本。
- 工艺参数控制
- 电压与电流:喷枪电压设定在60-90kV,电流根据粉末类型调整,避免“反电离”现象。
- 喷涂距离:保持15-30cm距离,过近易产生火花,过远导致粉末反弹。
- 烘烤曲线:采用阶梯式升温(如80℃/10min→120℃/10min→180℃/15min),防止涂层内应力集中。
- 前处理工艺
- 除油:采用碱性清洗剂或超声波清洗,去除工件表面油污。
- 磷化:锌系磷化膜厚度控制在2-3μm,提高涂层与基材的结合力。
- 干燥:工件表面水分需完全挥发,否则会导致涂层起泡。
三、优势分析:性能与成本的双重优化
- 附着力强化:静电吸附使粉末深入工件表面微观凹槽,结合磷化处理形成的化学键,涂层附着力可达0级(GB/T 9286标准)。
- 均匀性提升:电场力作用抵消重力影响,复杂形状工件(如管材内壁)涂层厚度偏差可控制在±5μm以内。
- 环保效益:粉末利用率高达95%,VOCs排放接近零,符合RoHS、REACH等环保法规。
- 经济性:单件涂装成本较液体涂料降低20-30%,尤其适合大批量生产。
四、优化方向:智能化与功能化趋势
- 智能喷涂系统:集成机器视觉与AI算法,实时调整喷涂参数,实现自适应控制。
- 低温固化技术:开发UV固化或红外快速固化粉末,缩短生产周期至5分钟以内。
- 功能性涂层:通过纳米材料改性,赋予涂层自清洁、抗菌、导电等特殊性能。
- 3D打印集成:结合增材制造技术,实现复杂结构工件的一体化涂装。
结语
静电喷塑工艺通过静电吸附与热固化技术的深度融合,在涂层附着力与均匀性方面展现出显著优势。随着材料科学与自动化技术的进步,该工艺正朝着、智能、多功能化方向发展,为制造业转型升级提供关键技术支撑。企业需持续优化工艺参数、升级设备性能,以在激烈的市场竞争中占据先机。